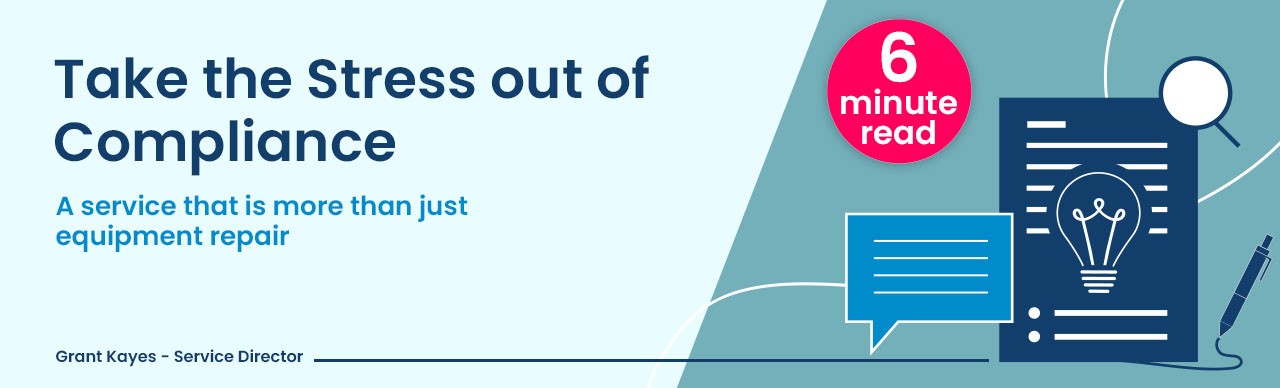
Take the stress out of compliance, with a service that is more than just equipment repair
By Grant Kayes - Service Director
In our profession, equipment aftercare support is not always at the forefront of our minds when making that initial purchase.
What’s the purchase price? Does the product have the right specifications for my intended application? Of course, these are very important questions.
Of equal importance, we want to consider whether is there an equipment aftercare support supplier behind this product in the UK? What’s the size of the aftercare support team? Are they the OEM? What’s the anticipated attendance time to avoid delays, and be back fully operational promptly? What costs are associated with the equipment aftercare support plans.
With all of that considered, that’s the real total cost of ownership.
So, at Burtons, we recognise and understand how busy a Veterinary practice can be, without the added worry or complication in managing equipment compliance whilst ensuring staff safety.
Our support plans are designed to alleviate these concerns. We’ll contact your practice team directly when equipment is due its next service or inspection, providing you with detailed comprehensive digital certification on completion. In the event your equipment malfunctions during those planned preventative maintenance schedules then you can contact our Service Team via telephone, email or online for reactive repairs.
Below are just five important HSE regulations which support the need and importance of routine equipment maintenance plans.
IRR17
Radiography Support
Any employer who undertakes work with ionising radiation must comply with the Ionising Radiation Regulations 2017. Equipment maintenance and inspection programmes are therefore an essential part of the employer’s duty of care and adhering to compliance of regulation 11.
The Burtons radiography team are there to support you and your employees by offering installation, demonstration, service, and or, repair across our range of Imaging products. We understand our customers require quick resolutions to such critical, clinical equipment, keeping down times to an absolute minimum, so the use of remote access technology is always our first preferred diagnosis option to get you back up and running as quickly as possible. Should you require a site visit, following remote diagnosis, then your localised radiography field technician will attend promptly to minimise operational downtime.
Our radiography after care support plans do not just support you through issues but also support the routine use of your equipment, giving you continued access to regular software updates, technical support across various platforms, loan equipment and preferential service charges.
Read more about our radiography support here
PUWER Regulations
PUWER requires that equipment provided for use at work is:
- Suitable for the intended use
- Safe for use, maintained in a safe condition and serviced or inspected to ensure it is correctly installed, operating as intended and does not subsequently deteriorate.
- Used only by operators who have received adequate information, instruction, and training.
- Used in accordance with the specific requirements.
Establishing a planned maintenance programme may be a useful step towards reducing risk, as well as having a reporting procedure for operators who may notice problems while working with the equipment.
- You must have arrangements in place to make sure the necessary service and inspections take place by a ‘competent person’.
The term 'competent person' is also used in certain legislation including PUWER. Although 'competent person' is not defined in law, the Approved Code Cf Practice broadly describes the attributes of a ‘competent person’ for undertaking Service & Repair works.
You should ensure that the person carrying out a such work has such appropriate practical and theoretical knowledge and experience of the equipment as well as being able to detect defects and to assess their importance in relation to the safe and continued use of the equipment. A high degree of competency of that person to bring the equipment safely back into active service through service and repair is therefore essential.
Read more about our most common compliance plans here
WAGS & WELS
Waste Anaesthetic Gases and Workplace Exposure Limits
Where anaesthetic gases are used in the workplace environment, there is a risk that volatile gases can escape into the atmosphere, causing potential harmful effects due to repeated exposure of low-level concentrations.
Side Effects? These gases can cause side effects, such as nausea, dizziness, headaches, fatigue and more - Good Health & Safety practice requires you to monitor and manage the safety of your staff by conducting occupational exposure monitoring to measure the RISK.
Scav - SAFE is an effective and convenient way to perform personal air sampling for many organic vapors, checking for any pollutants is vital to ensure the health and safety of you and your staff. So how does it work? Containing a simple charcoal sorbent wafer for easy collection. Simply order your badge kit, wear the clip-on badge as instructed in the manual provided, return the badge, and wait for your results.
Read more about our waste gas monitoring badges here
Pressure Systems Safety Regulations 2000
Written scheme of examination
Under the Pressure Systems Safety Regulations 2000, users and owners of pressure systems must demonstrate that they know the safe operating limits (principally pressure and temperature) of their systems, and that they are safe under those conditions. They need to ensure that a suitable written scheme of examination is in place before operating the system. They also need to ensure that the system is examined in accordance with the written scheme of examination.
During your annual or bi-annual autoclave service our Burtons engineer, as a competent person, can review your current written scheme of examination to ensure all aspects of the pressure system and its components are free from defect or failure to prevent hazards or serious injury.
With a burtons service plan, you can ensure that all your lifting equipment is always compliant with the regulations and ensure that your staff are using it safely. Not only does this protect your staff members, but it also helps to extend the life of your equipment, ensuring any issues are caught early and addressed before it becomes faulty or dangerous to use.
These are just 3 examples of how a Burtons service plan can help to take extra weight off your shoulders and guide you in ensuring the safety of you and other staff members. It also gives us a chance to find faults before they become an issue, keeping any equipment downtime to an absolute minimum.
LOLER
Lifting Equipment Inspections
‘Lifting Operations and Lifting Equipment Regulations’ and ‘The Provision and Use of Work Equipment Regulations.’
If you are an employer or self-employed person providing lifting equipment for use at work, or you have control of the use of lifting equipment, then the LOLER Regulations will apply to you. As an employer you need to demonstrate that you have effective maintenance programmes in place to make sure any lifting equipment is maintained in a safe condition.
‘LOLER’ regulations require lifting equipment to be strong and stable enough for use, and marked to indicate the maximum safe working loads. They also determine whether the equipment demonstrates minimal risks and that it is used safely as intended. Each service will have a check list to ensure all mechanisms of the lifting device are functioning well, without defects. These factors need to be examined and inspected by experts.
Read more about our most common compliance plans here
You can also contact the Burtons Service Team to find out more on 01622 834350